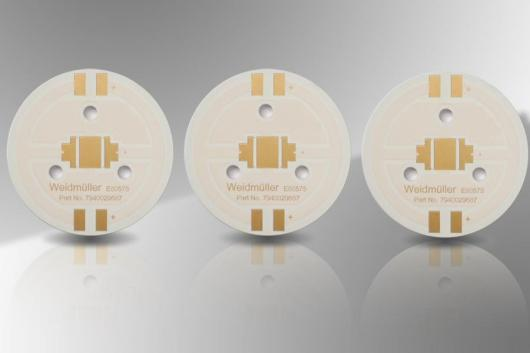
What is a substrate
The basIC material of manufacturing is the substrate, we generally say what is the substrate, refers to the substrate is copper clad laminate.
Nowadays, it has become an indispensable component of most electronic products. Single and double sided printed boards are manufactured in the substrate material - Copper clad foil laminate (Copper-(2lad I. Aminates, CCI.) Above, selective processing of hole processing, electroless copper plating, electroplating copper, etching, etc., to obtain the required circuit graphics. Another kind of multilayer printed board is also made of thin copper clad foil board with inner core. Conductive graphic layer and sEMI-cured sheet (Pregpr 'EG) are bonded together alternately by one-time lamination, forming inter-layer interconnection of more than three conductive graphic layers. Therefore, it can be seen that, as the substrate material in the manufacturing of printed board, both copper clad sheet and semi-solidified sheet play a very important role in the printed board. It has the function of conducting, insulating and supporting. The performance, quality, processability, cost and level of manufacturing of printed board depend greatly on the substrate material.
开云·kaiyun官方网站 substrate
Classification of substrate
Substrate materials for printed boards can be divided into two categories: rigid substrate materials and flexible substrate materials. An important type of general rigid substrate material is copper clad plate. It is made of Reinforeing Material, DIPped in resin adhesive, dried, cut, laminated into a blank, then covered with copper foil, using steel plate as mold, and processed by high temperature and high pressure forming in a hot press. The general multilayer plate with semi-cured piece, is the copper clad plate in the production process of semi-finished products (mostly glass cloth dipped in resin, after drying processing).
There are a variety of classification methods for copper clad foil panels. Generally, according to the different reinforcement materials of the board, it can be divided into: paper base, glass fiber cloth base, composite base (CEM series), laminated multilayer plate base and special material base (ceramic, metal core base, etc.) five categories. If the resin adhesive used by the plate is different for classification, the common paper based CCI. There are: phenolic resin (XPc, XxxPC, FR 1, FR 2, etc.), epoxy resin (FE 1 3), polyester resin and other types. Common glass fiber fabric CCL has epoxy resin (FR-4, FR-5), it is currently the most widely used type of glass fiber fabric. In addition, there are other special resins (glass fiber cloth, polyamide fiber, non-woven fabric, etc.) : biSMAleimide modified triazine resin (BT), polyimide resin (PI), diphenyl ether resin (PPO), maleic anhydride imide - styrene resin (MS), polycyanate resin, polyolefin resin, etc.
According to the classification of CCL flame retardant performance, it can be divided into flame retardant type (UL94 VO, UL94 V1 class) and non-flame retardant type (UL94 HB class) two types of board. In recent one to two years, with more attention to environmental issues, a new type of CCL without bromine has been separated from the flame retardant CCL, which can be calLED "green type flame retardant CCL". With the rapid development of electronic products technology, cCL has higher performance requirements. Therefore, according to the performance classification of CCL, it can be divided into general performance CCL, low dielectric constant CCL, high heat resistance CCL(general plate L is above 150℃), low thermal expansion coefficient CCL(generally used for packaging substrate) and other types.
Substrate cleaning method
Substrate cleaning methods can be summarized as mechanical cleaning and chemical cleaning.
Mechanical cleaning
Mechanical cleaning means cleaning with brush machine. Brush machine is divided into abrasive brush roller brush machine and pumice whitewashing machine two.
Abrasive brush roller type plate brush machine
Abrasive brush roller brush machine assembly brushes usually come in two types, compression brush and stiff brush. Compression brush is a very fine-grained silicon carbide or alumina abrasive bonded to the nylon wire, and then the nylon wire into fiberboard or cushion, after curing, cut into circular pieces, mounted on a roller core to make a brush roller. The body of the stiff brush is wound with 0.6mm diameter nylon wire containing silicon carbide abrasive. The abrasive size is different, and the purpose is different. Generally, the brush size of 180 mesh and 240 mesh are used for deburring treatment after drilling, and the brush size of 320 months and 500 mesh are used for substrate treatment before sticking dry film. The two kinds of brushes have their own advantages and disadvantages. Compression brush because of abrasive particle size is very fine, and brush roller on the surface of the brush plate pressure is larger, so the brush copper surface uniform, mainly used for cleaning the inner layer of multilayer plate substrate. Its disadvantage is due to the thin nylon filament easy to tear, short service life. The significant advantage of the stiff brush is the good wear resistance of nylon wire, so the service life is long, about ten times that of the compressed brush, but this brush should not be used to deal with the inner substrate of the multilayer plate, because the substrate is thin, not only the treatment effect is not ideal, but also cause the substrate curling. In THE process OF USING brush roller brush machine, in order to prevent nylon wire overheating and melting, should be sprayed on the board surface for cooling and wetting water.
Pumice stone whitewashing machine
Abrasive brush roller brush machine is widely used at home and abroad over the years. Research shows that with this kind of brush machine cleaning treatment plate surface is some lack, such as in the surface of the directional abrasion, there are cultivated grooves, sometimes the edge of the hole is torn to form an elliptical hole, because the grinding brush wear brush height is inconsistent and caused by the treatment of uneven surface. With the development of electronic industry, modern circuit design requirements of more and more fine line width and spacing, still use abrasive brush roller brush plate processing, product pass rate is low, so the development of pumice whitewashing machine. Pumice whitewashing machine is to spray pumice powder suspension to the surface of the board with a nylon brush to brush, the machine mainly has the following several sections: A. Nylon brush and pumice slurry liquid phase combined to brush; B. Scrub and remove pumice powder from the board surface; C. High pressure water washing; D. washed; E. dry.
Pumice whitewashing machine processing board surface has the following advantages:
A. Abrasive pumice powder particles combined with nylon brush is tangent to the surface of the brush, which can remove all dirt and expose fresh and pure copper;
B. Can form a completely sanded, rough, uniform, multi-modal surface, without plough-type grooves;
C. The connection between the surface and the hole will not be damaged due to the softening effect of the nylon brush;
D. Due to the flexibility of the relatively soft nylon brush, it can make up for the uneven surface problem caused by brush wear;
E. The image resolution is improved by reducing the scattering at exposure time because the board surface is uniform and unfurled. The disadvantage is that pumice powder is easy to damage the mechanical part of the equipment.
Chemical cleaning
Chemical cleaning begins with alkali solution to remove oil stains, fingerprints and other organic dirt on the surface of copper. Then, the oxide layer and the protective coating on the original Copper substrate to prevent the oxidation of copper were removed by acid solution. Finally, the coarsely coarsed surface with excellent adhesion property to the dry film was obtained by micro-etching treatment.
The advantages of chemical cleaning are that less copper foil is removed (1 to 1.5μm), the substrate itself is not affected by mechanical stress, and the treatment of thin plates is easier to operate than other methods. However, chemical treatment needs to monitor the change of chemical solution composition and adjust, and waste solution needs to be treated, which increases the cost of waste treatment. Engaged in the dry film production have to stick to the dry film test and research, the ideal surface with a 3) method to deal with the above 1) after the board face, put a dry film printing etching and graphics applications of electroplating for larger line width and spacing, no matter use which kinds of cleaning methods, pass rate tends to 100%, but when the line width of 90 mm, With pumice stone whitewashing machine treatment, the qualified rate decreased to 90%, other methods successively decreased, the worst decreased to 60%.
Electrolytic cleaning
Dry film substrate surface cleaning before, generally USES the above 1 a 2 kind of processing method, mechanical cleaning and pumice paint surface to remove chromium passivation membrane on the surface of the substrate (antioxidant) copper foil surface effect is good, but easy to scratch the surface, and may cause the abrasive particles (e.g., silicon carbide, alumina, pumice) embedded in the matrix, At the same time, it may also make the size of flexible substrate, laminated plate and thin printed circuit board substrate deformation. Chemical cleaning can remove oil pollution well, but the effect of removing chromium-containing passivation film is poor.
Electrolytic cleaning can not only solve the advantages of mechanical cleaning, pumice paint plate and chemical cleaning of the substrate surface cleaning problems, and make the base board produces a relatively even micro rough surface, greatly improve the specific surface, enhance dry film and the adhesive force on the surface of the substrate, the production of high density, thin wire conductive graphics is very beneficial.
The process of electrolytic cleaning is as follows: feed → electrolytic cleaning → water washing → microetching → water washing → passivation → water washing → drying → discharge
The main function of electrolytic cleaning is to remove oxides, fingerprints, other organic stains and chromium-containing passivates on the surface of copper foil.
The main effect of microetching is to make the copper foil form a microscopic rough surface to increase the specific surface. The role of passivation is to protect the coarsened fresh copper surface and prevent surface oxidation. Electrolytic cleaning is mainly used for surface cleaning treatment of flexible substrate, multilayer plate inner sheet and thin printed circuit board substrate before sticking dry film or coating liquid photoresist. Although it has many advantages, it is ineffective for cleaning epoxy stains on copper foil surface, and the cost of wastewater treatment is also high. According to the data reports, USA AtotechInc. (ChEMCut) has launched CS - 2000 series of horizontal anodic electrolytic cleaning equipment in the early 1990s, and also sells SchercleanEcs series of electrolytic cleaning agent.
The cleanliness of the treated board should be checked. The SIMple test method is the water film rupture test. After SLIDING treatment, THE board IS soaked with running water and placed vertically. The continuous water film on the whole board should be able to hold for 15 seconds without breaking. After cleaning treatment, it is best to immediately put the film, if the time of placing more than four hours, should be cleaned again
然后
联系
电话热线
13410863085Q Q
微信
- 邮箱