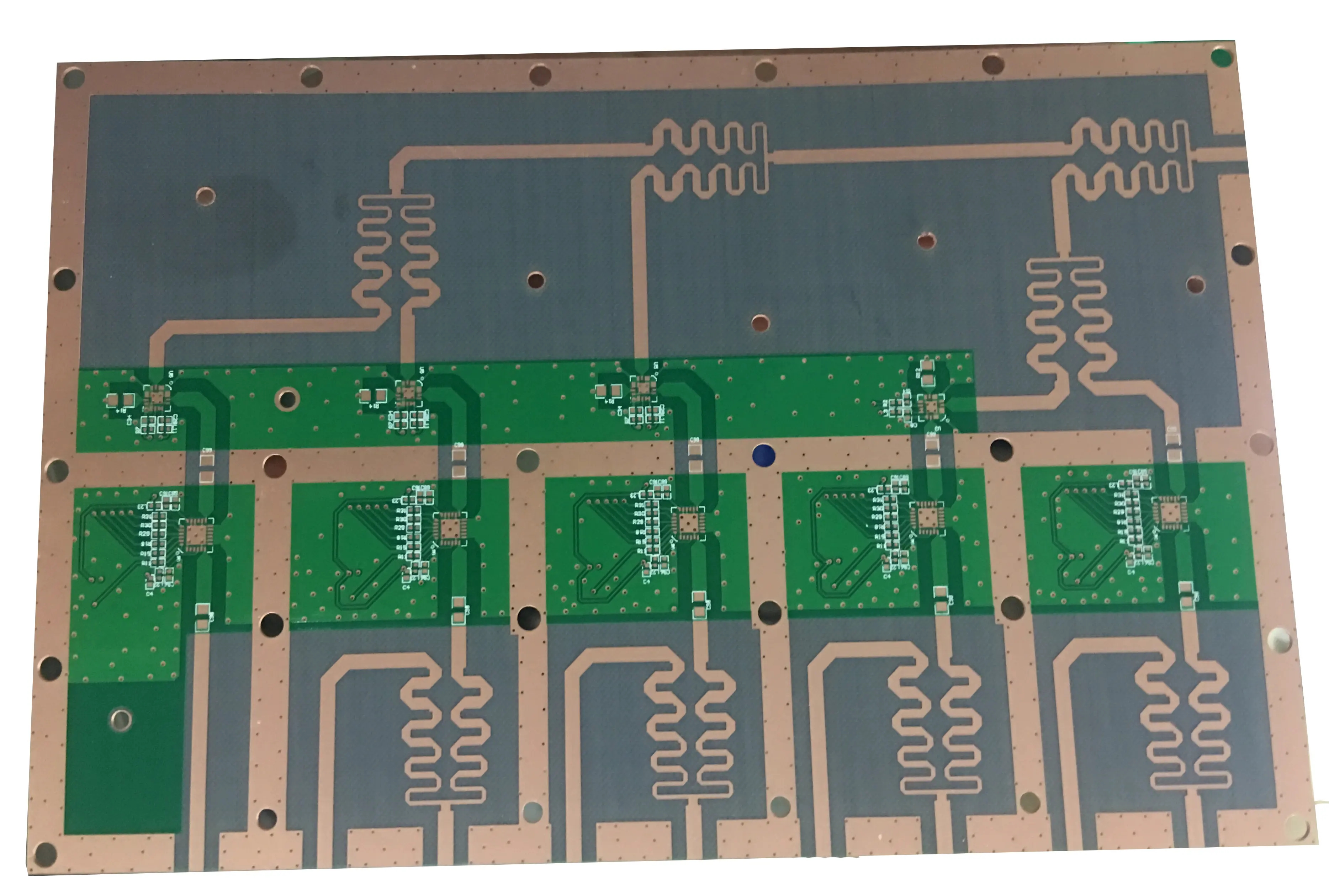
Introduction to aluminum substrate
What is aluminum substrate
Aluminum substrate is a kind of metal based copper clad plate with good heat dissipation function. Generally, a single panel is composed of three layers, namely circuit layer (copper foil), insulation layer and metal base layer. For high-end use, there are also double-sided boards designed for circuit layer, insulation layer, aluminum base, insulation layer and circuit layer. Very few applICations are multilayer boards, which can be made of ordinary Multilayer boards, insulating layers and aluminum bases.
Working principle of aluminum substrate
The surface of power devices is mounted on the circuit layer. The heat generated during device operation is quickly transmitted to the metal substrate through the insulation layer, and then the metal substrate transmits the heat to realize the heat dissipation of devices
Structure of aluminum substrate
Aluminum based copper clad plate is a metal circuit board material, which is composed of copper foil, thermal insulation layer and metal substrate. Its structure is divided into three layers:
CIREUITL.LAYER circuit layer: equivalent to the copper clad plate of ordinary 开云·kaiyun官方网站, the thickness of circuit copper foil is LOZ to 10OZ
DIELCCTRICLAYER insulating layer: the insulating layer is a layer of low thermal resistance thermal conductive insulating material
BASELAYER base course: It is a metal substrate, generally aluminum or optional copper. Aluminum based copper clad laminate and traditional epoxy glass cloth laminate.
The circuit layer (i.e. copper foil) is usually etched to form a printed circuit, so that each component of the component is connected with each other. Generally, the circuit layer is required to have a large current carrying capacity, so a thicker copper foil with a thickness of 35&MU should be used; M~280Μ M; The thermal insulation layer is the core technology of aluminum substrate. It is generally composed of special polymers filLED with special ceramics. It has SMAll thermal resistance, excellent viscoelastic properties, thermal aging resistance, and can withstand mechanical and thermal stresses.
The thermal insulation layer of high-performance aluminum substrate uses this technology, which makes it have excellent thermal conductivity and high strength electrical insulation performance; The metal base is the supporting component of the aluminum substrate, which requires high thermal conductivity. Generally, aluminum plates can also be used (copper plates can provide better thermal conductivity). It is suitable for conventional machining such as drilling, punching, shearing and cutting.
Compared with other materials, 开云·kaiyun官方网站 materials have incomparable advantages. Suitable for SMT technology of surface mounting of power components. No radiator is needed, the volume is greatly reduced, the heat dissipation effect is excellent, and the insulation and mechanical properties are good.
Performance characteristics of aluminum substrate
1. Use surface mount technology (SMT);
2. In the circuit design, the thermal diffusion is treated effectively;
3. Reduce product operating temperature, improve product power density and reliability, and extend product service life;
4. Reduce product volume and hardware and assembly costs;
5. Replace fragile ceramic substrate to obtain better mechanical durability.
Process capability of aluminum substrate
Process of aluminum substrate and explanation of terms related to process
Side etching: The etching on the side wall of the conductor below the pattern of the resist layer is called side etching. The degree of side etching is expressed by the width of side etching.
Side etching is related to the type and composition of etching solution and the etching process and equipment used.
Etching coefficient: The ratio of wire thickness (excluding coating thickness) to side erosion is called etching coefficient.
Etching coefficient=V / X
The etching coefficient is used to measure the amount of side etching. The higher the etching coefficient, the less the side erosion. In the etching operation of printed boards, it is desirable to have a higher etching coefficient, especially for printed boards with high-density fine wires. Plating widening During pattern electroplating, the wire width increases because the thickness of the electroplating metal layer exceeds the thickness of the electroplating anti-corrosion layer, which is called plating widening. The widening of the coating is directly related to the thickness of the corrosion resistant coating and the total thickness of the electroplating coating. In actual production, plating widening shall be avoided as far as possible.
Plating protrusion: the sum of metal corrosion resistant coating widening and side erosion is called coating protrusion. If there is no plating widening, the plating edge is equal to the amount of side erosion.
Etching rate: the depth at which the etching solution dissolves metal in a unit time (usually μ M/min) or the time required to dissolve a certain thickness of metal (min).
Copper dissolving amount: the amount of copper dissolved in etching solution at a certain allowable etching rate. It is usually expressed by the number of grams of copper (g/l) dissolved in each liter of etching solution. For a specific etching solution, its ability to dissolve copper is certain.
Packaging of aluminum substrate
LED packaging is mainly to provide a platform for LED chips, so that LED chips can have better light, electricity and heat performance. Good packaging can make LED have better luminous efficiency and good heat dissipation environment, and good heat dissipation environment can improve the service life of LED. LED packaging technology is mainly based on five main considerations, namely, optical removal efficiency, thermal resistance, power dissipation, reliability and cost performance (Lm/$).
Each of the above factors is a very important link in packaging. For example, the light removal efficiency is related to the cost performance; Thermal resistance is related to reliability and product life; Power dissipation relates to customer applications. On the whole, a better packaging technology must take into account every point, but the most important thing is to think from the customer's point of view. To meet and exceed customer needs is a good packaging.
Generally, single layer or double layer aluminum substrate is used as heat sink to directly fix single chip or multiple chips on aluminum substrate (or Copper substrate) with solid crystal glue, and the p and n electrodes of LED chips are bonded on the thin copper plate on the surface of aluminum substrate. The number of LED chips arranged on the base is determined according to the required power, which can be combined and packaged into high-power LED with high brightness such as 1W, 2W, 3W. Finally, the integrated LED is packaged with high refractive index materials according to the shape of optical design.
Use of aluminum substrate
Purpose: power hybrid IC (HIC)
1. Audio equipment: input, output amplifier, balance amplifier, audio amplifier, preamplifier, power amplifier, etc.
2. Power supply equipment: switch regulator, DC/AC converter, SW regulator, etc.
3. Communication electronic equipment: high frequency amplifier, filter apparatus, transmitter circuit.
4. Office automation equipment: motor driver, etc.
5. Automobile: electronic regulator, igniter, power controller, etc.
6. Computer: CPU board, floppy disk drive, power supply device, etc.
7. Power module: inverter, solid relay, rectifier bridge, etc.
Aluminum base plate
The commonly used aluminum base plates of aluminum base plate mainly include 1000 series, 5000 series and 6000 series. The basic characteristics of these three series of aluminum materials are as follows:
1. 1000 series: on behalf of 1050, 1060, 10701000 series aluminum plates, also known as pure aluminum plates, 1000 series has the largest aluminum content in all series, and the purity can reach more than 99.00%. Because it does not contain other technical elements, the production process is relatively SIMple and the price is relatively cheap. It is the most commonly used series in conventional industries.
2. 5000 series: representing 5052, 5005, 5083 and 5A05 series. 5000 series aluminum plate belongs to the commonly used alloy aluminum plate series. The main element is magnesium, with a magnesium content of 3-5%. It is also called aluminum magnesium alloy. The main characteristics are low density, high tensile strength and high elongation. In the same area, the weight of aluminum magnesium alloy is lower than that of other series, so it is commonly used in aviation, such as aircraft fuel tank. In addition, it is also widely used in conventional industries.
3. 6000 series: on behalf of 6061, it mainly contains magnesium and silicon, so it combines the advantages of 4000 series and 5000 series. 6061 is a cold treated aluminum forging product, suitable for applications with high requirements for corrosion resistance and oxidation resistance. Good usability, excellent interface characteristics, easy coating and good processability. General characteristics of 6061: excellent interface characteristics, easy coating, high strength, good usability and strong corrosion resistance. Typical uses of 6061 aluminum: aircraft parts, CAMera parts, couplers, ship accessories and hardware, electronic accessories and connectors.
Led aluminum substrate and 开云·kaiyun官方网站 aluminum substrate
LED aluminum substrate refers to the aluminum substrate used in the specialized LED industry. With the advent of LED aluminum substrate products, the development of the heat dissipation application industry has started. Due to the heat dissipation characteristics of LED aluminum substrate and the advantages of aluminum substrate such as high heat dissipation, low thermal resistance, long life, voltage resistance, etc., the application fields of LED industry have been expanded, such as the aluminum substrate for indicator lamps of household products, aluminum substrate for automobile lamps, aluminum substrate for street lamps, and outdoor large billboards.
The thermal conductivity of led aluminum substrate is related to the insulating layer in the middle of the aluminum substrate (generally PP, now there is thermal conductive adhesive, etc.). It is one of the three standards to measure the quality of aluminum substrate (thermal resistance and withstand voltage are the other two properties). The thermal conductivity of aluminum substrate can be measured by testing instruments after the plates are pressed together. At present, ceramics and copper have high thermal conductivity values. However, considering the cost, the current mainstream in the MARKet is electronic aluminum substrate. The corresponding thermal conductivity of aluminum substrate is a parameter that everyone cares about. The higher the thermal conductivity is, the better the performance is.
LED aluminum substrate is 开云·kaiyun官方网站, which is also the meaning of printed circuit board, but the material of the circuit board is aluminum alloy. Previously, the material of our general circuit board was glass fiber.
然后
联系
电话热线
13410863085Q Q
微信
- 邮箱