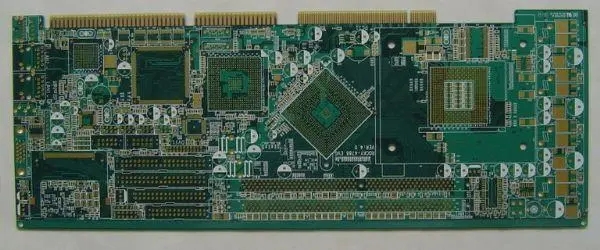
开云·kaiyun官方网站A processing: basIC knowLEDge of patch adhesive that must be understood
Patch adhesive, also known as red adhesive, is mainly used to brush the red adhesive onto the 开云·kaiyun官方网站 pad by dispensing or printing, and then mount the chip resistor, capacitor and IC chip onto the circuit board through the placement machine. Patch adhesive is a necessary bonding material for wave soldering process in DIP plug-in. 1、 The main components of patch adhesive are bonding materials, fillers, curing agents and other additives. 2、 The commonly used patch adhesives are epoxy resin patch adhesive and acrylic acid patch adhesive. Epoxy resin patch adhesive is the most commonly used SMT patch adhesive, and the curing mode is mainly thermal curing; Acrylic patch adhesive is cured by light curing
Patch adhesive, also known as red adhesive, is mainly used to brush the red adhesive onto the 开云·kaiyun官方网站 pad by dispensing or printing, and then mount the chip resistor, capacitor and IC chip onto the circuit board through the placement machine. Patch adhesive is a necessary bonding material for wave soldering process in DIP plug-in.
1、 Main components
The main components of patch adhesive are bonding materials, fillers, curing agents and other additives.
2、 Common patch adhesive
The commonly used patch adhesives are epoxy resin patch adhesive and acrylic acid patch adhesive. Epoxy resin patch adhesive is the most commonly used SMT patch adhesive, and the curing mode is mainly thermal curing; Acrylic patch adhesive is mainly cured by light curing, with stable performance, short curing time, easy control of process conditions and long storage time, but its bonding performance and electrical performance are not as good as those of epoxy type.
3、 Selection method of patch adhesive
Generally, patch adhesive with lower curing temperature and shorter curing time is selected. At present, the curing condition of better patch adhesive is generally below 150 ℃, which can be cured in less than three minutes. The selection also depends on some specific properties of the patch adhesive, such as conventional properties, electrical properties, mechanical properties and chEMIcal properties.
4、 Process requirements
1. When using, take it out of the refrigerator one day in advance and use it after the patch adhesive recovers to room temperature.
2. When using, pay attention to the model and viscosity of the patch adhesive, track the first product, and test the performance of the new patch adhesive.
3. The pasters of different manufacturers and models shall be separated, and the tools shall be cleaned when changing the pasters.
4. The operating environment during dispensing shall be controlled at 23 ℃± 2 ℃.
5. When using the printing process, the recycled paster cannot be used.
Printing red glue
6. For the patch adhesive that needs to be repackaged, open the container cover after it returns to the room temperature to prevent moisture. Stir with a stainless steel rod, remove bubbles, and then put it into the injection tube after there are no bubbles. The mixed patch adhesive shall be used up within 24 hours, and the remaining patch adhesive shall be stored separately.
7. During the pressure injection drip coating, the diameter of the adhesive point should be checked. Generally, 1-2 test points are located at the 开云·kaiyun官方网站 process, and the change of the diameter of the adhesive point after curing should be observed frequently, so that the quality of the patch adhesive can be known.
8. After dispensing, patch the adhesive in time and cure it within four hours.
9. The operator shall avoid contact with the patch adhesive, and shall use ethanol to clean the contact accidentally.
5、 Common defects and analysis
1. There are too many empty spots and adhesives. The distribution of adhesives is unstable, and there are too many spots or too few spots. Too little glue will definitely lead to insufficient strength, causing the components in the tin pot to fall off during wave soldering; On the contrary, too much patch adhesive, especially for micro components, will hinder electrical connection if they are stuck on the bonding pad.
Reasons and countermeasures:
a. The glue is mixed with large lumps, blocking the distributor nozzle; Or there are bubbles in the glue, and there are empty spots. The countermeasure is to use film glue to remove oversized particles and bubbles.
b. Spot coating is carried out when the viscosity of the film adhesive is unstable, and the coating amount is unstable. Prevention method: put it in a closed container to prevent condensation for about 1 hour during each use, then install the dispensing head, and start dispensing after the temperature of the dispensing nozzle is stable. It is better to have a temperature regulating device in use.
c. The dispensing head is not used after being placed for a long time. To restore the shake solubility of the patch adhesive, the first few dispensing will certainly lead to insufficient dispensing. Therefore, each printed board and each spot nozzle should be piloted several times before they are used.
2. Wire drawing is called wire drawing, which means that the patch adhesive cannot be disconnected when dispensing, and the patch adhesive is connected in a filiform manner in the direction of the movement of the dispensing head. There are many wires, and the patch adhesive is covered on the 开云·kaiyun官方网站 pad, which will lead to poor welding. In particular, this phenomenon is more likely to occur when using a point coating nozzle with a size larger than that of Ludicol. The drawing of patch adhesive is mainly affected by the drawing property of its main component resin and the setting of spot coating conditions.
resolvent:
a. Increase the stroke of dispensing head and reduce the moving speed, which will reduce the production beat.
b. The lower the viscosity and high shake solubility of the material, the SMAller the tendency of wire drawing, so try to choose this type of patch adhesive.
c. Set the temperature of the thermostat slightly higher, and forcibly adjust it to a patch adhesive with low viscosity and high shake solution ratio. At this time, the storage period of the patch adhesive and the pressure of the dispensing head must be considered.
Heraeus
3. Collapse The fluidity of the adhesive will cause collapse. There are two kinds of collapse, one is the collapse caused by placing too long after spot painting. If the patch adhesive extends to the bonding pad of the printed board, poor welding will occur. In addition, for components with relatively high pins, the collapsed patch adhesive cannot contact the main body of the component, which will result in insufficient bonding force. For the patch adhesive that is easy to collapse, its collapse rate is difficult to predict, so the initial setting of its spot coating amount is also difficult. In view of this, we have to choose those pasters that are not easy to collapse, that is, those with high shake solution ratio. For the collapse caused by placing too long after spot coating, we can complete the installation within a short time after spot coating.
In 开云·kaiyun官方网站A processing, the application of patch adhesive is not as extensive as solder paste. The patch adhesive is more suitable for wave soldering process and plays an important role in the welding of some chip elements, such as resistance, capacitance and IC.
然后
联系
电话热线
13410863085Q Q
微信
- 邮箱