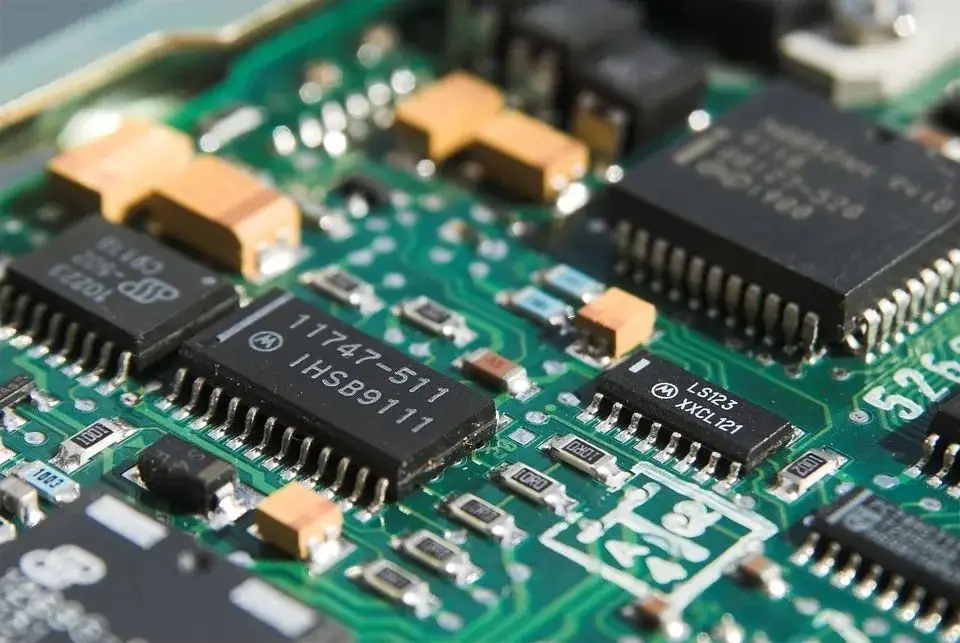
开云·kaiyun官方网站 technology Skills of 开云·kaiyun官方网站 Proofing Based on GENESIS 2000 Software
1、 Shape making
There are two ways to make shapes:
1 PhotographIC file by customer
Production steps:
A. Select the line border of the component surface with Select by net in the panel, and copy it to the rout layer;
B Delete all arcs;
C Check the number of lines, for example, there should be four lines in a rectangle, and delete the redundant lines;
D. Check the angle of the line. The angle of the conventional line should be 0 °, 90 ° and 45 °. If it is 0.1 °, it is mostly the customer's design error, and the MARKeting department should be consulted for handling opinions;
E Use the ROUT → Connections function to reconnect the line intersection and chamfer, and the arc line attribute should be arc;
F Change the line width to r10mil.
2 Dimension by customer
Steps of 开云·kaiyun官方网站 proofing:
A Create a route layer in Matrix;
B Select item 5 in Options → Line parameters;
C Use the Add feature function in the panel to manually draw the shape in the route layer according to the size marked by the customer, and set the line width to r10mil;
D Use the ROUT → Connections function to assist in connecting the line intersection and chamfering to the completion of the profile.
E If the ROUT layer has entities such as Rect or Oval, it needs to be converted into contour lines. Method: First select an entity and click Edit à Reshape à contour to change it to Surface, execute Surface to outline, and then enter the line width value to convert it to contour.
After the profile is completed, use the Select by net command to select the profile, and then use the Edit → Create → Profile command to create a profile.
Second orig production
The orig production consists of the following three parts:
1st floor alignment
Production steps:
A Select all layers, take the drilling hole as the reference layer, and use the register function to realize automatic alignment of lines, geoelectricity, resistance welding and drilling holes;
B Other layers (including character layer) need to move the whole layer manually to make the outer frame coincide with the outer frame of the line layer on the component surface. If necessary, it needs to be mirrored.
Inspection method:
A. The pad center of each layer shall be aligned with the drilling center;
B The outer frames of each layer shall overlap with each other;
C The characters on the component face are orthographic, and the characters on the welding face are reversed.
2 line to pad
Steps of 开云·kaiyun官方网站 proofing:
A Open the Features Histogram of the solder mask, select all in the Lines List, press Highlight, and judge whether to turn the pad according to the lines and characters;
B Select and open component surface line and component surface resistance welding at the same time, press W command to display the skeleton ↖ Select the line to be converted (generally the end of the line), and then use the DFM → Cleanup → Construct pads (Ref.) function to convert one by one. The method of welding surface is the same;
C Use the method in step a to check that all lines except the border line and large area tin spraying block have been converted;
D If an r-shaped line is converted to an oval shaped pad, use the Actions → Reference Selection function to select all ovals of the line layer with reference to the solder mask, remove the ovals covered by the solder mask layer (the same number as the solder mask layer ovals), and use the Edit → Reshape → Break command to interrupt the return line of the remaining ovals, and finally move the removed ovals back to the line layer. This operation should be used with caution when there is a positive negative superposition.
3 Define SMD
With the function of DFM → Cleanup → Set SMD attribute, the parameter Types Other is set to *, and the padlands without holes in the outer circuit are automatically set to SMD.
Delete the original edit in the Matrix and copy orig as edit. Unless otherwise specified, the following operations shall be performed in edit.
Three Matrix production
Take the standard 4-layer board as an example, define the properties of each layer, and use the X command to sort the layers according to the board making sequence. (Table 1)
Board drill positive
Board route positive
Component face characters board Silk_ screen positive
Resistance welding board solver_ mask positive
Board signal positive
Stratum board power_ ground negative
Electric board power_ ground negative
Board signal positive
Resistance welding board solver_ mask positive
Welding surface characters board Silk_ screen positive
1 The basis for correct arrangement of levels is as follows:
A The customer provides the hierarchical arrangement order;
B There are layer marks outside the board;
C. There are digital symbols in the board, such as "1, 2, 3, 4...".
2 The general basis for judging whether each layer is positive or negative is:
If the pad center is solid, it is positive; if the pad center is hollow, it is negative.
Four hole editing
1 Drilling process
A Open the Drill Tools Manager and check whether the hole diameter, hole number and hole attribute in the drilling file are correct against the drilling map provided by the customer. If there is no drilling map, the drilling file shall prevail;
B Change the via attribute of SMAll aperture and irregular distribution from plt to via;
C Input the hole diameter corresponding to each hole according to the Drilling Tool Compensation Rules;
D. Analyze the drilling layer with the function of Analysis → Fabrication → Drill Checks, and check whether the analysis results are abnormal;
E If there are multiple holes, use the NFP Removal function, and select Duplicate for the parameter Delete to automatically remove the duplicate of the drilling hole and the corresponding layer;
F If there are cross holes, manually delete the smaller vias in the cross holes and the corresponding pads of each layer; In case of device hole crossing, it cannot be deleted. Two pre drilLED holes tangent to the cross hole shall be added at both ends of the cross hole. Theoretically, the pre drilled hole diameter=(center distance of the cross hole+cross hole diameter)/2, and then the hole diameter shall be selected by tail removal method (in principle, the existing hole diameter in the plate shall be selected). For example, the aperture of two cross holes is 2.15mm, the center distance is 1.00mm, and the calculated aperture is 1.575mm, then the pre drilled aperture is 1.55mm.
2. Fabrication of drilling groove
A In the drilling layer, use the Edit → Reshape → Change Symbol command to change the required drilling groove shape to oval, for example, the drilling groove is 3.00X1.00, and the shape is oval 3X1;
B Use the Edit → Reshape → Break command to break oval into a line;
C If the length width ratio of the required drilling groove is less than 2, two pre drilled holes shall be added at both ends of the groove in the same way as the cross hole.
V. Preparation of Borehole Outline Drawing
Steps of 开云·kaiyun官方网站 proofing:
A Use the Edit → Copy → Other Layer command to copy the route layer to the new layer's tmp, and increase 5mil;
B In the tmp layer, use the Add feature function to mark the complete and correct overall dimensions. The width of the dimension line and extension line is r5mil, the arrow is special symbol → jian/jian45, and the dimension value is Text
The parameters are all 80 mils by XY, and the line width is 5 mil;
C Use the Create Drill Map function to automatically generate a drilling map, the unit is mm, and the drilling map is named map;
D Move all figures in the tmp layer to the map layer, and move the explanatory text in the customer's drilling map to the map layer, and merge it into the drilling outline drawing;
E Delete the tmp layer.
Six line layer fabrication
1 Delete the graphics outside the board
A Select all the board layers except the route layer, and use the ↖ Select profile borders one by one and delete
Division;
B Using the Clip Area function, select profile for the parameter Method, and select outside for the parameter Clip area, and automatically delete the graphics outside the board;
C Check and delete the shapes with uncluttered slab edges.
2 Overhanging surface pasting
A Select the component surface line layer, open the Feature selection filter function in the panel, select smd in the Attributes, and press select to select all surface stickers of the component surface line layer;
B Remove all the surface pastes of the line layer on the component surface to a new layer of gtl, and check whether the number of pads remaining in the line layer on the component surface is equal to the number of holes drilled. If the number is equal, it proves that the definition of the surface paste attribute is complete. If it is not equal, find out the pads whose surface paste attributes are not defined, select the Edit → attributes → Change function, select smd in the attributes, and then press OK to manually define the remaining surface paste and move it to the gtl layer;
C Move all graphics of the gtl layer back to the line layer of the component surface. If SMD needs to be compensated, it can be increased as required while moving;
D Select the component surface, add 11mil to all surface pastes of the line layer, and copy to the new layer D10
E Find out the identification point in the R-shaped D-code of D10 layer, determine the location of the identification point, add a copper ring to the identification point on the circuit board edge of the component surface, the outer diameter of the copper ring is 1mm larger than the inner diameter, and the inner diameter is 1mm larger than the resistance welding window of the identification point, so as to avoid touching the surrounding graphics;
F The fabrication method of the line layer on the welding surface is the same as above.
3 Line width compensation
A Select all the line layers, open the Feature selection filter function in the panel, close the Pads, Surfaces, Text and Negative elements buttons, press Select to select all the lines to be compensated, and then use the Edit → Resize → Global function to increase. See b for the increased value of impedance control line, which shall be compensated separately according to the impedance requirements.
4-plate alignment
Select all the board layers, and use DFM → Pad Snapping function to align the pads of each layer with reference to the drilling layer. If the offset is more than 2mil, the pads will not move. The production personnel should propose.
5 Optimization of wire layer hole pad
A Select the circuit layer of the component surface, use the DFM → Signal Layer Opt function, and optimize the pads according to the default parameters. Check the optimization results. If the ARG navigation (min) report appears, it indicates that some pads are not optimized due to insufficient spacing. Undo this optimization step first, then open the column chart to check whether the hole diameter of the pad that is not optimized belongs to Via or Plt, and then reduce the land parameters corresponding to this hole level by level with 0.5mil, and re optimize until the optimization is completed. Maintain the existing parameters to optimize the line layer of the welding surface;
B The inner pad optimization method is the same as the outer pad optimization method;
C Move the circuit layer hole pad on the component surface to the gtl layer, change the attribute of the gtl layer to board+signal+positive, and re optimize the gtl layer pad with DFM → Signal Layer Opt function. The parameters PTH AR and VIA AR maintain the original settings, and the parameters Spacing and Drill to cu are changed to 0. After optimization, all figures in the gtl layer will be moved back to the component surface circuit layer. Repeat this procedure for welded faces.
Note: All outer layers use the same optimization parameters, and all inner layers also use the same optimization parameters. The parameters of outer layers and inner layers can be different.
6 Removal of non functional pads
A. Use the DFM → NFP Removal function to automatically remove the inner layer of unlined pads; Turn off the PTH and Via options in the parameter Drill, change the parameter Remove undrilled Pads to No, and automatically remove the outer NPTH pad;
F The welding surface D11 is made according to the same method, and the layer name is jobs-a.d11.
开云·kaiyun官方网站 manufacturing, 开云·kaiyun官方网站 design and 开云·kaiyun官方网站A processing manufacturers will explain 开云·kaiyun官方网站 technology skills of 开云·kaiyun官方网站 proofing based on GENESIS 2000 software.
然后
联系
电话热线
13410863085Q Q
微信
- 邮箱