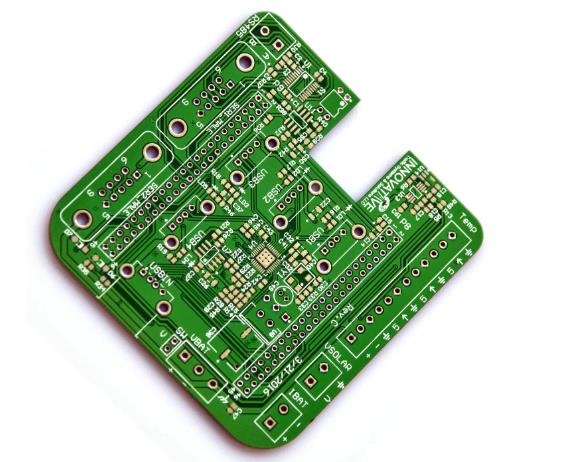
Lean production of circuit board manufacturers
32 pieces of introduction to lean production by circuit board manufacturers
1. What is Lean Production?
It refers to a new type of production mode that uses a variety of modern management methods and means, takes social needs as the basis, gives full play to the role of people as the basis, effectively allocates and reasonably uses enterprise resources, and maximizes economIC benefits for enterprises.
2. What is the goal of lean production?
Completely eliminate ineffective labor and waste, and maximize economic benefits for enterprises.
3. What is the core of Lean Production?
"Lean" means lean, "benefit" means benefit, and "lean" means less investment, more production, and elimination of waste.
4. What is the fundamental difference between lean production and mass production in thinking methods?
The endless pursuit of perfection in the business objectives of the enterprise.
5. What is the endless perfection goal pursued by lean production?
Low cost, scrap free, zero inventory and product diversification.
6. Why does our company implement lean production?
In order to improve labor efficiency, completely eliminate ineffective labor and waste, achieve maximum economic benefits, and improve the competitiveness of enterprises.
7. Is Lean Production only suitable for manufacturing departments (fields)?
No, it should also be extended to product development, collaborative support, sales services, financial management and other departments (fields), throughout the entire process of enterprise production and operation activities.
8. What are the characteristics of lean production?
A. Implement pull type just in time production, and eliminate all advanced and excessive manufacturing;
B. Short product development and production preparation cycle;
C. The main engine factory and the assisting factory have close relationship and common interests.
9. Where is the starting point of lean production?
The starting point of lean production is sales, and users are regarded as part of the manufacturing process.
10. What are the difficulties in implementing lean production?
The most difficult point is the change in ideology.
11. What are the main methods of lean production?
Just in time production, kanban management, leveling production, quick tooling change, standard operation, synchronous production, improvement activities, zero failure management of equipment, target cost, three no flow quality control method, etc.
12. What are the important components of lean production?
Organize pull (just in time) production, improve and improve labor organization and on-site management, and completely eliminate ineffective labor and waste in the manufacturing process.
13. What is effective labor and ineffective labor?
Labor that can add value and added value is calLED effective labor; Labor that cannot add additional value is invalid labor.
14. What is the basic method of lean production to organize the production process?
Use pull management to replace traditional push management.
15. What is the core of pull production?
It is just in time, that is, it is required to produce the required products and the required quantity when needed.
16. To produce ahead of time and overfulfil tasks is a sign of high labor efficiency. It should be effective labor, right?
No, overproduction is also a kind of ineffective labor and waste.
17. Since handling is a waste, should the factory completely cancel handling?
No, necessary handling is necessary in the factory, but it should be minimized.
18. What are the characteristics of the pull method?
First, adhere to the requirements of the next process, rather than interrupt production, and do not engage in excess production ahead of time. Second, the production order is not only a production plan, but also a micro adjustment with Kanban.
19. What are the main aspects of ineffective labor and waste in lean production?
A. Invalid labor caused by excessive production;
B. Waste of waiting;
C. Waste of handling;
D. Waste of action;
E. Waste of inventory;
F. Invalid labor and waste of processing itself;
G. Waste of manufacturing defective products.
20. How to solve the ineffective labor caused by excessive production?
Use just in time production and Kanban management to exclude.
21. How to eliminate the waste caused by waiting?
Adjust the division of labor and strictly organize production.
22. How to eliminate waste during handling?
Adjust the plane layout and reasonably organize the logistics.
23. How to eliminate the waste of actions?
Improve the station layout and operation method to reduce the waste of action.
24. What is "pull" production?
The so-called "pull" production means that the production of each process is pulled by the needs of the next process,
What to produce, how much to produce, and when to produce are all based on the prEMIse of meeting the needs of the next process.
25. What does the "three for system" in lean production mean?
The so-called "three for system" is to take the production site as the center, the production workers as the main body, and the workshop director as the head.
26. What is the group work method?
The group work method is that the production organization of an enterprise takes a group as a unit, which not only organizes production, but also participates in management and even management.
27. What are the responsibilities of SMAll groups in the "group work method"?
Complete production tasks, ensure product quality, control material consumption, replace and adjust jigs and fixtures, do well in equipment maintenance, and engage in on-site improvement.
28. What are the four main aspects of on-site operation standards?
The main contents of the operation standard include production rhythm, standard WIP, process procedures and quality.
29. What is the relationship between "5S" activities and lean production?
The "5S" activity is the basis of all management work. If the "5S" activity can not be done well, it can only be empty talk to promote lean production.
30. Is the operation standard in the lean production mode formulated by the on-site management (or functional department) or the production team leader? Where should the work be suspended?
It is mainly formulated by the production team leader and shall be hung on the operation site.
31. What is Kanban?
Kanban is a management method that can adjust and control the necessary quantity of necessary products produced at the necessary time.
32. What are the conditions for implementing Kanban management?
a. Must be based on assembly line operation;
b. Balanced production, good implementation of process procedures and processes, and process quality control;
c. Good equipment and tooling to ensure stable processing quality;
d. The quantity and quality of raw materials and outsourced and purchased parts are guaranteed;
e. Implement standard operation, and the plane layout of the production site is reasonable.
The above are 32 lean production lines explained to you by 开云·kaiyun官方网站 design, 开云·kaiyun官方网站 manufacturing and 开云·kaiyun官方网站 proofing manufacturers.
然后
联系
电话热线
13410863085Q Q
微信
- 邮箱